I’ve spent about 2 days on dealing with the ADC (Analog to Digital Converter) of the Arduino platform. Turns out there’s more problems to overcome when dealing with taking analog signal from a sensor and converting it to meaningful digital reading.
The issue is that even with a constant input voltage the ADC reading sampling error rate is larger than I’d like (~1.2%) with some random spikes in excess of 3%.
I built a test rig to troubleshoot the issue. Using constant input voltage and a potentiometer to simulate the analog input from a sensor.
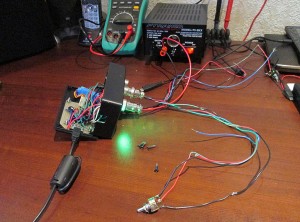
Goal:
– At least 4 sample updates per second. (Smooth gauge updates)
– Stable voltage regardless of outside interference.
Things I found:
– Arduino Atmel chip uses a single ADC and multiplexes the input pins.
– Switching read pin on the ADC causes noise in the system. Solution to read the first value and totally discard it. Then wait at least 10ms before sampling actual data.
– Sample accuracy is inversely proportional to the delay between samples. Shorter delay between reads, less drift. But over a static period of time, the error rate is the same.
– ADC is quite sensitive to electronic noise. Adjacent pins seem to affect reading.
Things I tried:
– Average voltage over multiple samples (currently 11 samples per read)
– Add delay between readings (1 to 12 ms) (currently 2ms)
– Discard top and bottom values and average the rest (currently discard 25%)
– Add a delta value, discard new value if difference is less than delta (currently 0.011V)
– vary delay on multiplex debounce (currently 10ms)
Current sampling rate: 3.7 samples / second.
Final Arduino Code:
const int LED_RED = 9;
const int LED_GREEN = 8;
const int LED_BLUE = 7;
const int LED_ACT = 11;
const int INPUT_REF = 22;
const int INPUT_RATE = 20;
int refPins[4] = {19, 17, 18, 16};
int sensePins[4] = {15, 13, 14, 12};
double lastRefVolts[4] = { 0, 0, 0, 0 };
double lastSenseVolts[4] = { 0, 0, 0, 0 };
const float LOW_VOLTAGE = 4.5; //alert voltage for 5V bus
const int MAX_SAMPLES = 50; //max sample on trim pot
const float DISCARD_PCT = 0.25; //percent of samples to discard (top and bottom)
const float MAX_DELTA = 0.011; //ignore changes less than this
const int SAMPLE_DELAY = 2; //delay MS between sample reads
const int INITIAL_DELAY = 10; //delay MS on pin change
void setup()
{
//set pin IO modes
pinMode(LED_RED, OUTPUT);
pinMode(LED_GREEN, OUTPUT);
pinMode(LED_BLUE, OUTPUT);
pinMode(LED_ACT, OUTPUT);
for (int pin = 0; pin < 4; pin++)
{
pinMode(refPins[pin], INPUT);
pinMode(sensePins[pin], INPUT);
}
pinMode(INPUT_REF, INPUT);
pinMode(INPUT_RATE, INPUT);
//cycle leds
digitalWrite(LED_RED, HIGH);
digitalWrite(LED_BLUE, HIGH);
digitalWrite(LED_GREEN, HIGH);
setLED(LOW, HIGH, HIGH);
delay(200);
setLED(HIGH, LOW, HIGH);
delay(200);
setLED(HIGH, HIGH, LOW);
delay(200);
setLED(LOW, LOW, LOW);
delay(200);
setLED(HIGH, HIGH, HIGH);
//emulated serial, speed ignored
Serial.begin(38400);
}
void loop()
{
//read serial to clear buffer
if (Serial.available() > 0)
{
Serial.flush();
}
//get number of samples to read
int readCount = getReadCount();
//write +5V bus voltage
writeRefVoltage(readCount);
//write all input sensors
for (int pin = 0; pin < 4; pin++) {
writeSerialVoltage(pin, readCount);
}
}
void writeSerialVoltage(int pin, int readCount)
{
digitalWrite(LED_BLUE, HIGH); //blue off - start sending
digitalWrite(LED_ACT, LOW); //internal off
//ref volt, seems more volatile
float refVolt = getVoltage(refPins[pin], readCount);
float newRefVolt = processRefVoltage(pin, refVolt);
//get sensor voltage
float senseVolt = getVoltage(sensePins[pin], readCount);
float newSenseVolt = processSenseVoltage(pin, senseVolt);
Serial.print("IN"); //write identifier
Serial.print(pin);
Serial.print("\t");
Serial.print(newRefVolt, 4);
Serial.print("\t");
Serial.print(newSenseVolt, 4);
Serial.print("\r");
Serial.println("");
digitalWrite(LED_ACT, HIGH); //internal on
digitalWrite(LED_BLUE, LOW); //blue on - sending done
}
//do a delta comparison on Ref voltage
float processRefVoltage(int Pin, float refVolt)
{
float lastRefVolt = lastRefVolts[Pin];
if (abs(refVolt - lastRefVolt) < MAX_DELTA)
refVolt = lastRefVolts[Pin];
else
lastRefVolts[Pin] = refVolt;
return refVolt;
}
//do delta comparison on sensor voltage
float processSenseVoltage(int Pin, float senseVolt)
{
float lastSenseVolt = lastSenseVolts[Pin];
if (abs(senseVolt - lastSenseVolt) < MAX_DELTA)
senseVolt = lastSenseVolts[Pin];
else
lastSenseVolts[Pin] = senseVolt;
return senseVolt;
}
//send bus voltage to host
void writeRefVoltage(int readCount) {
float refVoltage = getVoltage(INPUT_REF, readCount);
if (refVoltage < LOW_VOLTAGE)
{
digitalWrite(LED_RED, LOW);
digitalWrite(LED_GREEN, HIGH);
}
else
{
digitalWrite(LED_RED, HIGH);
digitalWrite(LED_GREEN, LOW);
}
Serial.print("REF\t");
Serial.print(refVoltage, 4);
Serial.println("");
}
//read value from ADC (0-1023) and convert to voltage (0-5)
float getVoltage(int PIN, int samples) {
//allow ADC to stablize
analogRead(PIN); //ignore value
delay(INITIAL_DELAY); //wait for debounce
float sampleList[samples];
//read samples
for (int i = 0; i < samples; i++)
{
float voltage = (float)analogRead(PIN) * (5.0 / 1024.0);
//round to 2 decimals
sampleList[i] = (ceil(voltage * 100.0)) / 100.0;
delay(SAMPLE_DELAY);
}
//sort array (shitty bubble sort, cause i'm lazy)
float swapper;
for (int o = samples-1; o > 0; o--) {
for (int i = 1; i <= o; i++) {
if (sampleList[i-1] > sampleList[i]) {
swapper = sampleList[i-1];
sampleList [i-1] = sampleList[i];
sampleList[i] = swapper;
}
}
}
//discard % of top and bottom values, average the rest
int avgStart = max(samples * DISCARD_PCT, 1); //array start
int avgEnd = min(samples * (1.0 - DISCARD_PCT), samples); //array end
int avgSamples = 0;
float ret = 0;
//average out the values
for (int cntr = avgStart; cntr < avgEnd; cntr++)
{
avgSamples++;
ret += sampleList[cntr];
}
return ret / (float)avgSamples;
}
//read trim pot, get average samples
int getReadCount() {
analogRead(INPUT_RATE);
int readCount = analogRead(INPUT_RATE);
return map(readCount, 0, 1023, 4, MAX_SAMPLES);
}
//set RGB led values
void setLED(int RED, int GREEN, int BLUE) {
digitalWrite(LED_RED, RED);
digitalWrite(LED_GREEN, GREEN);
digitalWrite(LED_BLUE, BLUE);
}
Binary sketch size: 7,196 bytes (of a 32,256 byte maximum)
Estimated memory use: 103 bytes (of a 2,560 byte maximum)
This is probably as close as I can get to get an accurate reading that doesn't jump around too much. Filters most noise while giving a decent sample rate. Currently reading all 4 inputs. Technically could reduce to 3 inputs since 4th won't be used for a while. Will see how well Gauge Pod software deals with current feed rate.